True Position Calculator
Our GD&T true position calculator will help you assess whether a part clears or fails a dimension inspection. More precisely, it will determine whether the axes of the bore and shaft lie within the tolerance zone from their true position in the drawing.
True position and position tolerancing are concepts used in geometric dimensioning and tolerancing (GD&T) to locate features on a part, especially groups of small holes. We know that GD&T can be a nightmare for beginners — bear with us, and we'll show you how position tolerancing can help you clear more parts than coordinate tolerancing!
In this article, we'll break down some fundamentals of position tolerancing for you, such as:
- What is position tolerance?
- How to calculate the true position of a hole using position tolerance.
- Material conditions and calculating bonus tolerance for true position.
💡 If you're interested in part design and engineering drawings, you'll find our taper calculator helpful.
How to calculate true position using this GD&T true position calculator
Our GD&T true position calculator is a versatile tool, and here's how to use it:
-
Provide the following details from the drawing's feature control frame:
- The position tolerance value; and
- The material condition.
-
If you select either MMC or LMC, enter the following:
- Select whether the feature is a hole or a shaft.
- Enter the feature's size along with its tolerance values.
-
Enter the true position according to the drawing by inputting the basic dimensions of the position from the secondary and tertiary datums (presumed to be B and C, respectively, but the naming doesn't matter).
-
Enter the dimensions as measured on the actual part. If either MMC or LMC is applicable, you must also give the actual feature size.
-
The calculator will generate a position offset summary, which includes:
- Offset of the position from the drawing's true position;
- Overall position variation;
- If applicable, the calculated bonus tolerance for the true position;
- Total tolerance; and
- Tolerance excess or deficit observed in the actual part.
True position, coordinate tolerancing and position tolerancing
We can use coordinate dimensions and tolerances to locate the center of a hole, like in the figure below:
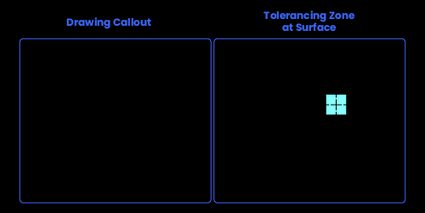
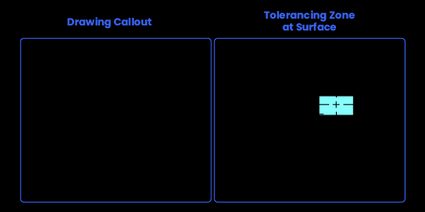
The true position of the hole's center (and the bore's axis) is its ideal location, as shown in the drawing. It is nearly impossible to achieve this position in manufacturing, especially when making multiple parts. That is why the drawing includes tolerance limits. The actual center of a manufactured part can lie anywhere within this tolerance zone.
🙋 What do we mean by "calculating the true position of a hole"?
The true position is already specified in the drawing. So, by "calculating true position", we mean to check whether the actual position on a manufactured part lies close enough to the true position to be acceptable. In other words, we calculate the deviation from the true position, and whether it's within some tolerance.
Since the tolerance zones in coordinate tolerancing are square or rectangular, the maximum permissible error occurs along the diagonal.
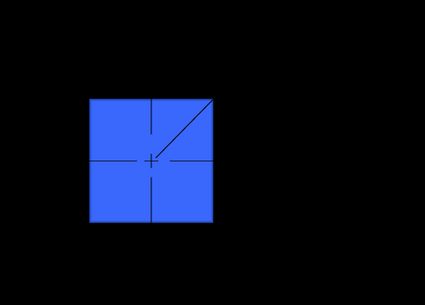
This maximum tolerance is given by:
💡 Learn how to calculate this as a square diagonal using our diagonal of a square calculator.
If the tolerance is ±0.20 inches in both directions, the maximum tolerance is:
You can see the problem here: The error along the diagonal is around 1.4 times higher than what is allowed in the horizontal or vertical direction. This means we would have to downsize our tolerance to about 0.7 times to ensure the maximum error stays within 0.20, which means tightening the tolerances along the horizontal and vertical directions! This problem is eliminated with position tolerancing, which we'll discuss next.
Position tolerancing is a form of geometric tolerancing where the tolerance zone (usually cylindrical) is defined directly around the true position, as shown below:
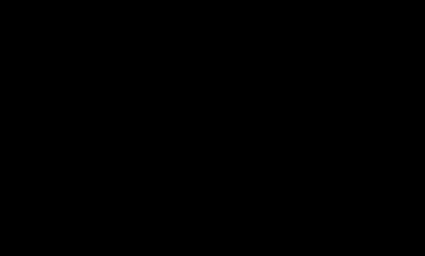
The main elements involved in "setting" a position tolerance zone are:
-
Basic dimensions that fix the true position of the hole's center;
-
Feature (hole) size with tolerance;
-
Feature control frame specifying the position tolerance; and
-
Datum planes from which the dimensions will be measured.
Let's take a closer look at the feature control frame:
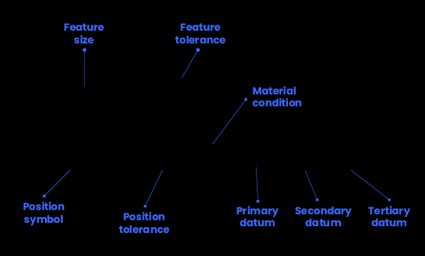
The functions of the various components in this frame are:
-
The GD&T position symbol indicates that this control frame refers to the feature's position.
-
The number following the diameter symbol is the diameter of the tolerance zone around the true position.
-
The material condition dictates what material condition applies to this feature. We shall discuss these conditions in a later section.
-
In order, the datum letters show this feature's primary, secondary, and tertiary datums.
Notice that, unlike coordinate tolerancing, position tolerancing gives a cylindrical site with equal tolerance in all directions! This allows us to specify the maximum permissible error in all directions, allowing for 57% more area in the tolerance zone! This makes a part more likely to be accepted without affecting the part's functional aspects.
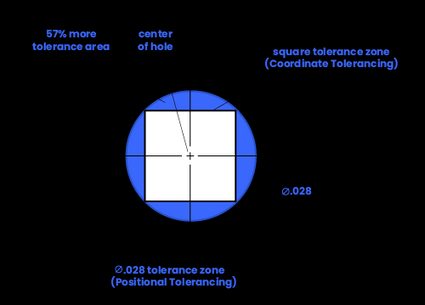
Formula for calculating true position of a hole or shaft
As we discussed in the previous section, when we say "how to calculate the true position of a hole", we want to calculate the variation between the true and actual positions.
Notice that the position tolerance is given as a diameter. So, we can use the distance formula to find the radial distance between the true and measured positions. We then double it before comparing it with the position tolerance.
The formula for calculating the actual position variation/deviation from the true position is:
where:
-
— Position variation from the true position;
-
— True position of the feature from datum B;
-
— Measured position of the feature on the part from datum B;
-
— True position of the feature from datum C; and
-
— Measured position of the feature on the part from datum C.
For the part to be accepted, it must meet the condition , where is the total position tolerance. When no material condition is specified, the position tolerance in the drawing directly applies to the part regardless of feature size. In such a case, the total position tolerance is equal to the position tolerance.
But when a material condition is given, bonus tolerances may be applicable based on the actual feature size. The next sections will discuss calculating true position tolerance for these cases.
What are the maximum and least material conditions?
When a feature on an actual part comes in a dimension that allows it to contain the most material possible, it is said to be in maximum material condition (MMC). The MMC is met for internal features like holes when the hole's diameter is the smallest possible value. The opposite is true for external features like shafts — MMC is met when the shaft has the largest possible diameter.
Similarly, when a feature's dimension allows for the least material possible, the least material condition (LMC) is satisfied. The LMC is met for internal features like holes when the hole's diameter is the largest possible value. The opposite is true for external features like shafts — LMC is met when the shaft has the smallest possible diameter.
Material conditions — Calculating bonus tolerance for true position
Often, the position tolerance may depend on the size of the feature on the actual part. For instance, it may be okay for the part to have a larger variation in the hole's center when it is bigger, but when the hole is on the smaller side, its center must fall within a tighter tolerance. So, when the hole is bigger on an actual part, the center's position tolerance can be "relaxed" by adding some bonus tolerance.
In some cases, the opposite may be true — where the feature's center can have a larger variation if the feature size falls on the smaller side, but when the feature size is larger, the tolerance applicable is "rigid".
Engineers can specify this dependency (or lack thereof) on the feature size using a material condition modifier in the feature control frame. The three material conditions we can use are:
-
for maximum material condition (MMC).
-
for least (or minimum) material condition (LMC).
-
No symbol to indicate the position tolerance applies regardless of feature size (RFS).
Depending on the condition specified, we must calculate the bonus tolerance for the true position.
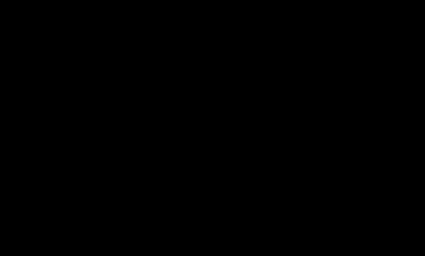
To understand how to calculate the true position for the MMC condition, let's look at the position tolerance example again. On an actual part, the hole diameter can be as small as 0.502 in or as large as 0.508 in. At the same time, the drawing contains the symbol for MMC. This means the hole's center gets more tolerance if its diameter is large.
The following table shows the possible diameters and the respective tolerance values.
Actual hole size | MMC size | Bonus tolerance | Position tolerance | Total tolerance |
---|---|---|---|---|
0.502 | 0.502 | 0.000 | 0.028 | 0.028 |
0.503 | 0.502 | 0.001 | 0.028 | 0.029 |
0.504 | 0.502 | 0.002 | 0.028 | 0.030 |
0.505 | 0.502 | 0.003 | 0.028 | 0.031 |
0.506 | 0.502 | 0.004 | 0.028 | 0.032 |
0.507 | 0.502 | 0.005 | 0.028 | 0.033 |
0.508 | 0.502 | 0.006 | 0.028 | 0.034 |
Now, suppose the LMC condition was given instead of the MMC. The LMC size of the hole is 0.508. The tolerance values then would've looked like:
Actual hole size | LMC size | Bonus tolerance | Position tolerance | Total tolerance |
---|---|---|---|---|
0.502 | 0.508 | 0.006 | 0.028 | 0.034 |
0.503 | 0.508 | 0.005 | 0.028 | 0.033 |
0.504 | 0.508 | 0.004 | 0.028 | 0.032 |
0.505 | 0.508 | 0.003 | 0.028 | 0.031 |
0.506 | 0.508 | 0.002 | 0.028 | 0.030 |
0.507 | 0.508 | 0.001 | 0.028 | 0.029 |
0.508 | 0.508 | 0.000 | 0.028 | 0.028 |
If no symbol was present, the RFS condition would apply, and the hole center's tolerance would be 0.028 regardless of the hole size.
To summarize, the MMC bonus tolerance calculation formula is:
While the LMC bonus tolerance formula would be:
Needless to say, the bonus tolerance for RFS is:
So, when calculating true position tolerance, we need to consider the material condition and augment our true position calculation formula with the bonus tolerance:
FAQs
How do I calculate true position bonus tolerance?
To calculate the bonus tolerance of the true position, follow these steps:
-
Inspect the drawing to find the material condition applicable to the feature.
- If no material condition symbol is specified, the bonus tolerance is zero.
-
Obtain the MMC size (or LMC size) of the feature from the drawing.
-
Measure the feature size on the actual part.
-
If MMC is applied, subtract the MMC size from the actual size.
-
If LMC is applied, subtract the LMC size from the actual size.
-
-
Obtain the absolute value of this difference to get the bonus tolerance.
How do I calculate MMC for the true position?
To calculate the true position tolerance for MMC, follow these steps:
-
Obtain the MMC size of the feature from the drawing.
-
Measure the actual feature size in the part.
-
Subtract the MMC size from the actual size.
-
Take the absolute value of this difference to obtain the bonus tolerance.
-
Add this bonus tolerance to the position tolerance to get the total position tolerance.
Head to our true position calculator for further details or examples.
How do you select primary datum feature for position tolerancing?
When selecting primary datum for holes, the surface into which the hole is drilled is usually chosen. This will help ensure that the hole remains perpendicular (or at the required angle if the hole is not perpendicular). In the case of long holes, it may be functionally essential that a hole remains parallel to a side rather than perpendicular to a face. If so, one may choose the relevant side as the primary datum.
What is the bonus tolerance if the hole diameter is 0.254 and the MMC size is 0.246?
The bonus tolerance when the hole diameter is 0.254, and the MMC size is 0.246 is 0.008. We must use this formula:
bonus tolerance
= actual size - MMC size
= 0.254 - 0.246
= 0.008